Carbon Film Resistors
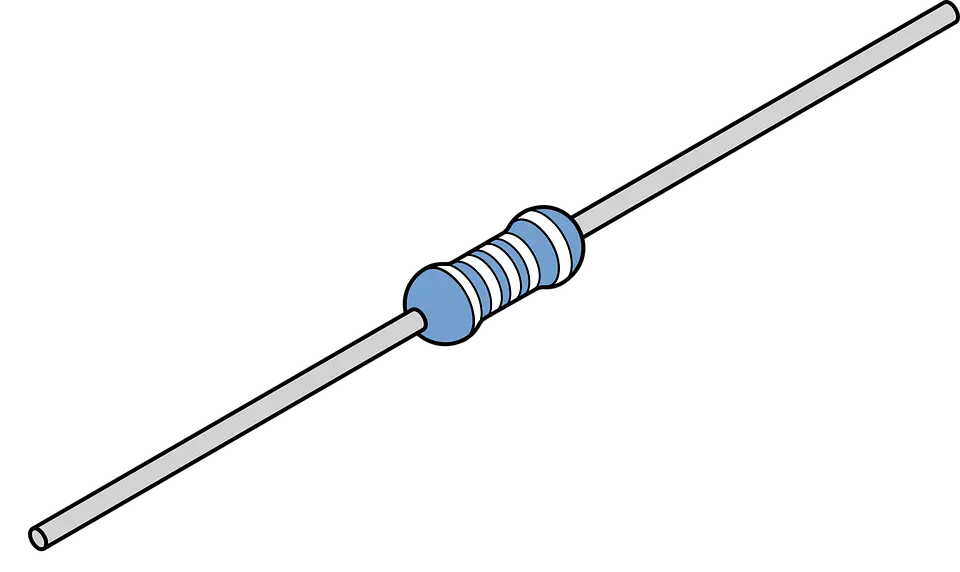
A carbon film resistor is a type of electrical resistor that is made by depositing a film of conductive carbon particles onto a substrate and cutting a long, helical conductive path to determine resistance value.
The value of the carbon film resistor, as well as its’ other properties, depends on several factors. These include the thickness of the film, the length, and the width of the conductive path.
Resistors were first invented in 1959 by the German electrician Otis Boykin and have undergone countless innovations since. The basic premise behind a resistor is to ‘resist’ the flow of electric current. To make this possible, resistors are made of electric conductors such as compressed carbon and metal. Since all conductors have some resistance (except for superconductors, which have zero resistance), manufacturers can use the properties of conductors to produce a resistor with a specific value of resistance.
There are many types of resistors, including carbon composition, wirewound, metal and carbon film resistors. This guide will take an in-depth look at carbon film resistors.
What is a Carbon Film Resistor?
A carbon film resistor is prepared by depositing a carbon film on an insulating substrate. This is followed by cutting a helix shape to create a path of varying degrees of resistivity. Designers can use varying shapes and resistivity of amorphous carbon to provide a wide range of resistance values. An automatic machine is used to create further spirals of the resistive coating until the resistance between the two ends of the resistor reaches the correct value.
The length of the resistor and its width are two major factors that can be precisely controlled with tight tolerances of under 1%. Carbon film is superior to carbon composition because of low noise and the precise distribution of graphite. This provides long-term stability and low tolerance to the resistor and a wide operating range.
Carbon film resistors only provide a single resistance value. The resistor’s accuracy depends on the helical cut made into the film.
Carbon film resistors will always have the same value of resistance regardless of the frequency of supply from DC. The value of Ohms is always positive in nature and never negative.
Like other types of resistors, carbon film resistors often use color coding on the body to allow the value to be quickly identified.
How Are Carbon Film Resistors Manufactured?
The thermal deposition process is used to manufacture carbon film resistors. This process requires a few steps:
- A ceramic rod is placed at extremely high temperatures and pressures
- A hydrocarbon gas, usually benzene or methane, is passed over the rods at temperatures of 1000°C
- The hydrocarbon gas breaks down at this temperature
- A coating of carbon is deposited onto the rods
- A manufacturing machine makes helical cuts in the carbon
- The value of the resistance can be altered by optimizing the length of the helical path (based on the proportional relationship between resistance and length).
The resistance value is inversely proportional to the width of the helical carbon film cut. Therefore, a cut with a smaller width will provide more resistance to the electric current because the current has to travel a larger distance through the resistive path. This also reduces the likelihood of collision of free electrons with atoms. A small number of free electrons collide with atoms, allowing the remaining electrons to freely move across the resistor. These electrons will carry electric current when they move from one place to another. This is why carbon film resistors with a larger helical carbon film cut allow more current to pass through.
In general, a carbon film resistor is made up of the following parts:
- A ceramic core (for insulation against heat and electricity)
- Lead
- Carbon film (to restrict the flow of current)
- Nickel cap
- Epoxy layer (to protect the resistor)
The primary role of the ceramic substance is to act as an insulator against heat and electricity. Ceramic allows the resistor to withstand extremely high temperatures without getting damaged. This property is particularly useful in electronic devices where temperatures may get high due to factors (such as unfavorable temperatures, restricted airflow, and stressful operational conditions).
Both ends of carbon film resistors are metallic. Copper is used as the metal of choice for making the two connecting leads,
Properties of carbon film resistors
In this section, we will explore the properties of carbon film resistors.
- The resistance range of carbon film resistors varies from less than 1Ω to 10MΩ
- The maximum noise is at 20 (QV/V) with a noise electromotive force under 10QV/V
- Nominal resistance E-48
- The accuracy of carbon film resistors ranges from 2% to 5%. The accuracy is subject to various factors.
- The voltage coefficient for carbon film resistors is 0.0005
- The tolerance availability for carbon film resistors is 32%, 35%, 310%, and 320%
- The maximum resistor temperature is 150°C
- In general, the larger their physical size, the greater their wattage rating (which is in the range of 0.25W, 0.250W, 0.5W, 1W, 2W, 5W, and 10W at a temperature of 70°C)
- The temperature coefficient varies from 3200 ppm/°C to more than 31,500ppm/°C.
- Carbon film resistors are noted for exhibiting high frequency (this is why they can be transformed to high frequency and ultra-high-frequency resistors )
- Carbon film resistors are packaged using bulk packaging or bagging
- Pulse stability in carbon film resistors is stable. They can adapt quickly to pulses (this allows for their use in DC circuits, AC circuits, and suit pulses).
- The maximum temperature for the resistor is 150°C
Advantages of Carbon Film Resistors
Carbon film resistors are superior to carbon composition resistors. Noise levels of the carbon film resistor are incredibly low because pure graphite (carbon) is used for distribution. Moreover, carbon film resistors tend to have a very high negative temperature coefficient than carbon composition – this can be a good or bad characteristic, depending on the application. In most cases, the resistive temperature coefficient may lie in the range of 2.5 ×10-4 Ω/°C and -8×10-4 Ω/°C.
For the most part, the operational temperature of carbon film resistors is up to 350 degrees celsius with a voltage of 15kV. The biggest advantage of carbon film resistors is their ability to withstand high-energy pulses. In addition, carbon film resistors are smaller in size than carbon composition resistors, thereby transporting them in greater quantities and easing the burden on overly taxed supply chains and logistics systems.
Disadvantages of carbon film resistors
Although carbon film resistors are a major improvement over carbon composition resistors, they have their fair share of limitations compared to metal film and metal oxide film. For starters, the resistance range for commercially available carbon film resistors is limited. Metal and metal oxide film resistors are less expensive and provide superior properties.
Moreover, these resistors are often used in electronics. Carbon film resistors may be impossible to implement in applications that require ultra-low sizes.
Carbon film resistors are very durable, but they lag in performance, making it difficult to recommend their usage in highly sensitive, modern electronic circuits. It also turns out that carbon may not resist moisture and humid conditions in the long run, or sustain normal operations in high-temperature conditions.
For example, carbon film resistors may not be used in the oil industry which is the largest consumer of electronic equipment in high temperatures. Deep exploration exposes the circuits to harsh environments that can be devastating to most types of film resistors, especially carbon film resistors.
This may sound confusing because carbon film resistors have a high negative temperature coefficient. However, while the devices can operate under high temperatures, their resistance decreases significantly with increased temperature.
They can become especially stressed during high voltage applications, which is often the case with surge protector devices. The result is a loss of performance stability. However, as long as they are used in appropriate applications, carbon film resistors are a great choice for reliable, durable resistors.
Finally, carbon film resistors require access to skilled technicians who possess a working knowledge of the devices for installation, maintenance, replacement, and diagnostics. This can increase overhead costs for a business in the long run.
Carbon film Resistor vs. Metal Film Resistor
The main difference between metal film and carbon film resistors is the use of a metal oxide film to coat the ceramic road. This thin metal film is used to limit the flow of electric current.
The construction phase of metal film resistors involves extracting an appropriate metal (usually nickel-chromium alloy, antimony, tin, and others). The film is aged by storing it at a low temperature for a long period.
The aging of metal film resistors is useful because it increases the accuracy of the resistor. Manufacturers control the accuracy and stability of metal film resistors by altering its overall thickness. Thicker metal film has higher stability but a lower accuracy and vice versa.
The resistance can be altered by making a spiral-shaped slot in the metal film with the help of a laser. Just like carbon film resistors, the ends of metal film resistors are also covered with metal. The higher the sum of antimony, the higher the resistance. Good resistance for metal film resistors relies on the thickness of the metal oxide and the width of the metal film cut.
Metal film resistors often make use of a protective coating and markings. The coating contains a resin reinforced with several layers and is also baked.
Metal film resistors have highly desirable characteristics for stability and tolerance. This allows them to be used in circuits where a low-temperature coefficient, low noise properties, and tight tolerance are very important. Examples of applications that use metal film resistors include bridge circuits and active filters.
Before we discuss the differences between carbon film and metal film resistors, it is important to learn about their similarities. These are as follows:
- Both types of resistors are very similar in terms of shape and appearance
- They are similar in size (although metal film resistors tend to be smaller on average)
- A ceramic core is utilized as a non-conducting material
- Resistance can be adjusted by changing the thickness of the film
The primary differences between metal film resistors and carbon film resistors can be summarized in the table below.
Metal Film Resistors | Carbon Film Resistors | |
Description | These resistors use a thin metal film to resist the flow of electric current. | These resistors use a thin carbon film to limit the flow of electric current. |
Construction | Metal film resistors have a thin metal film made of tin, nickel-chromium alloy, antimony, or others. This metal film coats ceramic. | Carbon film resistors have a thin carbon layer made out of pure graphite. The graphite coats ceramic. |
Tolerance | Metal film resistors often have better tolerance compared to carbon film resistors (cost dependent) | Carbon film resistors have worse tolerance compared with metal film resistors (cost dependent) |
Stability | Metal film resistors are very stable. | Carbon film resistors are not very stable. |
Cost | Metal film resistors are comparatively affordable. | Carbon film resistors are relatively expensive. |
Noise | Metal film resistors have a low noise design. | Carbon film resistors feature high noise design |
Tolerance | Metal film resistors boast tolerance levels as low as 0.1%. | Carbon film resistors have a minimum low tolerance level of 2%, which is several orders of magnitude inferior to metal film resistors. |
Size | Metal film resistors are smaller, making them a safer choice for most applications. | Carbon film resistors are larger. |
Because of these major differences in noise and tolerances, carbon film resistors and metal film resistors are not interchangeable. Swapping out a carbon film resistor for a metal film resistor of a similar resistive value could change how a circuit operates – and this may be bad for the device’s longevity. If a resistor is faulty, it is strongly recommended to swap it out with a similar resistor.
Most carbon film resistors are pink or yellow because of low accuracy and lower production costs. This is in strong contrast with metal film resistors that are blue in color. Carbon film resistors have a layer of black protective paint on their surface, while metal film resistors have a coating of bright white protective films.
Applications of Carbon Film Resistors
Carbon film resistors have revolutionized the electronic industry and can be credited as the single biggest reason for the unprecedented growth rate of technology. Moreover, because carbon film resistors can survive high energy pulses despite their small form factor, the tiny devices can be used to power everyday applications.
You will find almost universal use of carbon film resistors across electronic devices. In fact, chances are that you have already come across a carbon film resistor at some point in your life.
It is used in making the power supply systems for radar systems, X-rays, and lasers. Carbon film resistors are also used in industries that most people are familiar with. These usages can be categorized as:
Consumer Electronics
- Office gadgets such as personal computers, scanners, printers, and FAX machines
- Home appliances such as refrigerators, air conditioners, microwave ovens, and vacuum cleaners
- Audio and video systems such as microphones, loudspeakers, and VCRs
- Speaker systems make use of capacitors and carbon film resistors
Industrial Electronics
Carbon film resistors have been used in powerlifting many industries and helping with automation, robotics, and mechatronics. Key applications in the industrial sector include renewable energy, power electronics, photovoltaic systems, and biomechanics.
Environmental Monitoring
Meteorological devices that use various sensors are often designed using sophisticated electronic systems making use of carbon film resistors. Some of these include:
- Hygrometer to measure humidity
- Barometer to make weather predictions
- Data loggers are used to log important data related to the environment such as the temperature, solar radiation, humidity, and wind speed
- Drifter buoy to measure current, temperature, and pressure levels in the water
Medical Applications
Advanced instruments have been developed for medical applications that improve the healing process and the accuracy of diagnostics.
Some of the medical devices that use carbon film resistors include:
- Respiration monitor to monitor a patient’s health markers such as respiration, blood flow, body temperature, and pulse
- Stethoscope to detect the inner sounds occurring inside the human body
- A defibrillator sends electrical pulses to the heart and restores it back to normal working conditions
- Glucose meter to measure blood sugar levels
Carbon Film Resistor Symbol
There are several ways of identifying the resistive values of carbon film resistor symbols. The most common method of identifying the values is through color bands and color codes around the resistor’s body.
The symbol for carbon film resistors is a zig-zag line or a rectangular box. It is not uncommon to differentiate the type of resistor with the help of a prefix such as “CR.” For example, if a 140kΩ carbon film resistor is being used, it would be written as CR140kΩ to indicate the same.
Wrapping Up
Carbon film resistors have different applications based on their strengths and weaknesses. Their properties, like most film resistors, are subject to the environment. Designers who ignore the environmental threats facing carbon film resistors are at risk of increasing the failure rate.
It is recommended to understand the purpose of the electronic circuit and use a suitable resistor that can withstand the regular operating conditions of that particular environment. Most engineers struggle to choose the right type of resistor for their circuit. However, a good understanding of carbon film resistors and their close alternatives will help you make a more informed decision.